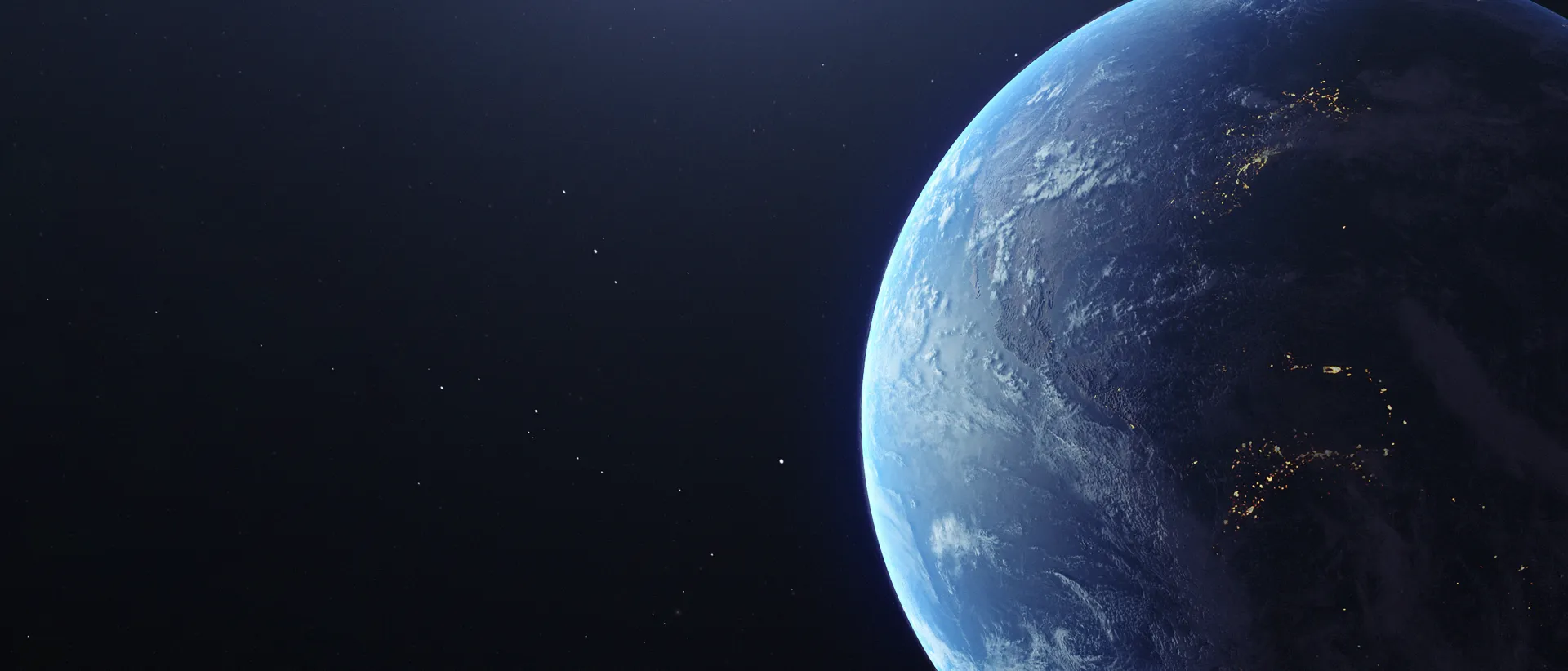
Customized Mechanisms
Beyond Gravity offers customized mechanisms, including rotary actuators, antenna pointing and deployment solutions, rotary damping devices, and fine-pointing assemblies. Our mechanisms are based on flight-qualified designs and can be quickly delivered to meet your mission schedule.
Beyond Gravity offers customized mechanisms, pre-developed solutions that can be adapted to meet the specific needs of space missions. These mechanisms are either full- or near-recurring with selectable performance characteristics, or they are custom-developed for complex missions.
Beyond Gravity customized mechanisms include rotary actuators with selectable gear ratio and power supply characteristics, mechanical solutions for antenna pointing and deployment, rotary damping devices, and fine-pointing assemblies. All of these mechanisms are based on flight-qualified designs and can be quickly delivered to meet your mission schedule.
Actuators
Electric propulsion pointing mechanisms (EPPMs) require actuators that are lightweight, precise, and reliable. Beyond Gravity offers a range of actuators that are optimized for use in EPPMs, including the Low-Cost Actuator 15 (LA15) and the Small Actuator 15 (SA15).
Low-Cost Actuator 15 (LA15)
Beyond Gravity offers a low-cost actuator (LA) optimized for minimal manufacturing and assembly costs. It features high unpowered detent torque, allowing it to maintain the pointing position in an unpowered state even under high back-driving torques.
The LA15 low-cost actuator is a hybrid-type stepper motor with high detent torque, a planetary gear, and high-load output bearings. It is based on the Beyond Gravity modular actuator system, which allows the full range of motors and gears in the system to be exploited to meet specific requirements.
The LA15 low-cost actuator will be used in Beyond Gravity electric propulsion pointing (EPPM) mechanisms.
Small Actuator 15 (SA15)
The Small Actuator SA 15 is a low mass actuator with high unpowered detent torque feature, maintaining its pointing direction in unpowered condition even under high back driving torques. It consists of a permanent magnet high detent torque stepper motor, a planetary gear, and high load output bearings. The SA 15 is based on the actuator built to drive the Aperture Cover of the Sentinel 4 instrument on the ESA Meteosat 3rd generation satellite. A total of 2 QMs and 7 FMs are built for the Sentinel 4 programme. The SA 15 is used in Beyond Gravity Electric Propulsion Pointing (EPPM) mechanisms.
Mirror Pointing Mechanisms
Mirror pointing mechanisms (MPMs) are essential components of space telescopes. They are responsible for precisely positioning and aligning the mirror(s) in order to focus light onto the telescope's detectors. Beyond Gravity offers a range of MPMs that are optimized for use in space telescopes.
Linear Refocusing Mechanism (REM)
The Linear Refocusing Mechanism (REM) is a critical component of the Main Optics Assembly of the Infra Red Sounder (IRS) and Flexible Combined Imager (FCI) instruments. It supports the M2 mirror and allows for precise on-ground pre-adjustment of position, keeps the mirror in position during launch, and allows for refocusing in-orbit.
The REM is essential for ensuring the high-quality images and measurements that the IRS and FCI instruments are designed to produce. It is also a highly reliable and robust mechanism, designed to withstand the harsh environment of space.
Secondary Mirror Focusing and Aligning Mechanism (M2M)
The Secondary Mirror Focusing and Aligning Mechanism (M2M) is a critical component of cryogenic telescopes such as EChO, ARIEL, and SPICA. It is designed to mitigate the risks associated with thermoelastic, manufacturing, ageing, and other on-orbit effects by providing precise focusing and alignment of the secondary mirror.
The M2M can be configured as either a 3DoF actuator-driven tripod or a 6DoF actuator-driven hexapod. The specific configuration is selected based on the specific requirements of the telescope.
Sentinel-4 Mission: Scanner Subsystem
Given the challenges that further increasing climate change poses for Europe, and its potentially enormous impact on our infrastructure and everyday life, we need a understanding of how exactly the climate may change in the future. How can we and our mechanisms help with climate monitoring? We will show you!
Deployment System for Large Appendages
Beyond Gravity has developed and qualified a spring-driven, non-reversible Deployment System for Large Appendages, which is focused on high position accuracy and stiffness in the deployed configuration. It also provides an integrated deployment damper to eliminate the end position latching shock. This Deployment System is intended for the deployment of large appendages such as large reflector antennas or solar arrays.
The deployment hinge features a locking mechanism to provide high position accuracy and stiffness in the deployed configuration, an angular contact ball bearing in O-arrangement for smooth and reliable operation, and a deployment range of up to 180°. This hinge can be modified to meet the specific needs of each customer, such as different dimensions, mass, and locking mechanisms.
Viscous Deployment Damper
The Viscous Deployment Damper is a lightweight and customizable solution for preventing high shock loads at the end stop of a deployment mechanism. The Viscous Deployment Damper consists of a housing and rotor. When the rotor is turned, it forces highly viscous working fluid through narrow gaps. The resistive torque thus generated eliminates the need for high ratio gears, which can be heavy and inefficient.
The Viscous Deployment Damper is available in versions for deployment angles up to 90° and up to 270°.
Antenna Pointing Mechanism
Beyond Gravity offers a tailorable Antenna Pointing Mechanism for all kind of RF communication in space that can be widely tailored to mission needs.